Historical context
The starting point of this collaboration between IBOIS, EESD and MANSLAB is the thesis “TIMBER+” of Andrea Settimi written in 2020 for EPFL-IBOIS. Settimi’s research focuses on vernacular constructions mixing timber and mineral components around the world. Some of these constructions are very well known like FACHWERKBAU/RIEGELBAU in Germany, or OPUS CRATICUM and MURUS GALLICUS described by Vitruvius in the roman time. There are many others we never heard about like DHAJI DEWARI from Pakistan, POMBALINO in Lisbon, KAT-KI-KUNNI in Himalach Pradesh - India, TAQ BHATAR in Nepal and Pakistan, to quote a few of them.
The load-bearing masonry with horizontal wood lacing, but without vertical reinforcement is the construction typology we are interested in. The buildings fabricated with this type of construction technique are known to have a strong resistance to seismic forces. This is provided by the combination of dry-stacked stone masonry, which has a high capacity for energy dissipation, and the timber bands with their excellent tensile and elastic properties (Dowling et al., 2007).
THE PROMISING POTENTIAL
- Seismic resistance earthquake-proved
- Low-tech technique
- Non transformed materials/ sustainable building material
- Circular and sustainable strategies
- Reduce consume of water in mineral constructions
- Economy of resources
- Using local resources (avoiding transport of material)
- Reduce embodied energy
- Easily repairable
- Down-cycling components
THE Research QUESTION:
- How can we understand the craft knowledge behind this construction technique and how can we replicate it with today's technology ?
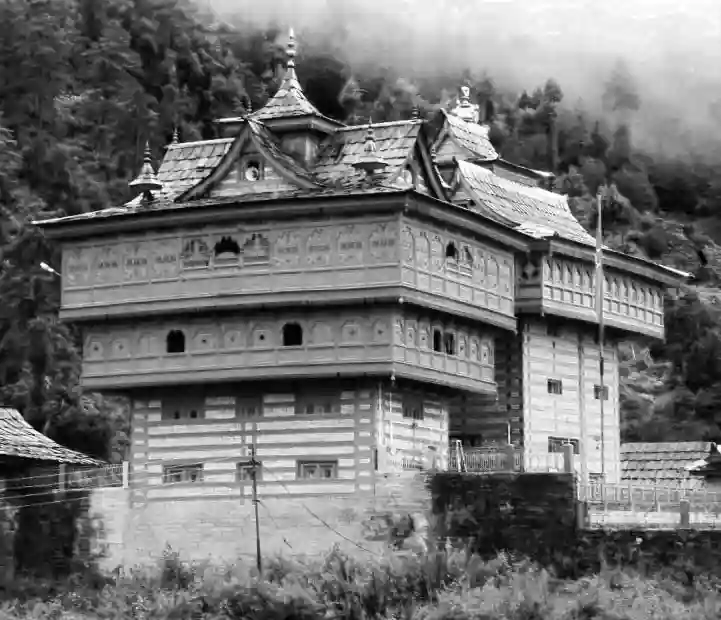
Students Mockups
Spring semester 2021 - EARTH
After filling the “Flon” river with a pile of rubble coming from the digging of the funicular connecting the Lausanne railway station to the city centre, the neighbourhood has hosted industrial purposes, then artistic and underground activities; nowadays restaurants and shops.
The students had to build a workshop where apprentices come to learn how to make gardening tools. This new construction interacts with the vicinity with the same economy of means: the experience of essential needs sublimate the perceptions of this powerful moment of planting. The rusticated character of timber-lace construction evokes a feeling of proximity to nature.
The students make 1:10 mock-up models with the purpose of researching for ingenious physical solutions: they construct significant walls out of timber and stones without the use of any mortar. The use of waste material, stacking or fill-in, different proportions of stone and wooden parts, prefabrication, etc. have been explored.
Building of the wall
Digital means have to learn from human gestures:
An experienced craftsman, Urs Lippert and his company Stonework’s Lippert gmbh in Evillard built a timber-laced wall of 1,5m length, 0,7m width and 1,5m height.
To push the economy of means to its extreme, the use of offcuts from a quarry interested us, but for Urs there is no waste in construction with dry stones. To fully grasp this idea, we asked him to build two walls: one with rock falls from Guber Natursteine and the other with stones selected by his expert eye from the Plasselb quarry. All his gestures have been photographed and filmed in order to be able to imitate his actions with digital means. To be able to scan the stones in place in 3D, we dismantled the stones one by one and again filmed and documented the position of each stone.
Digital Twin
The process of building the walls in laboratory conditions with expert craftsmen made it possible to reconstruct the first precise digital models of this vernacular building technique and explore in detail its composition.
To achieve this ambitious goal, the IBOIS research team developed an open-source tool for point cloud processing in computer-aided design called “Cockroach”. Based on LiDAR scans, the wall is digitally reconstructed layer by layer (see animation below) while the craftsmen build the wall. Later, the positioning of the stones and their exact geometries are retrieved with the help of the "Cockroach" tool (see layer 6).
This key stage of the project allowed us to archive for the first time an accurate 3D CAD model of this type of construction but also to obtain essential information (such as the geometry of the stones and their placement) for the following stages of the project (scroll down for more!).
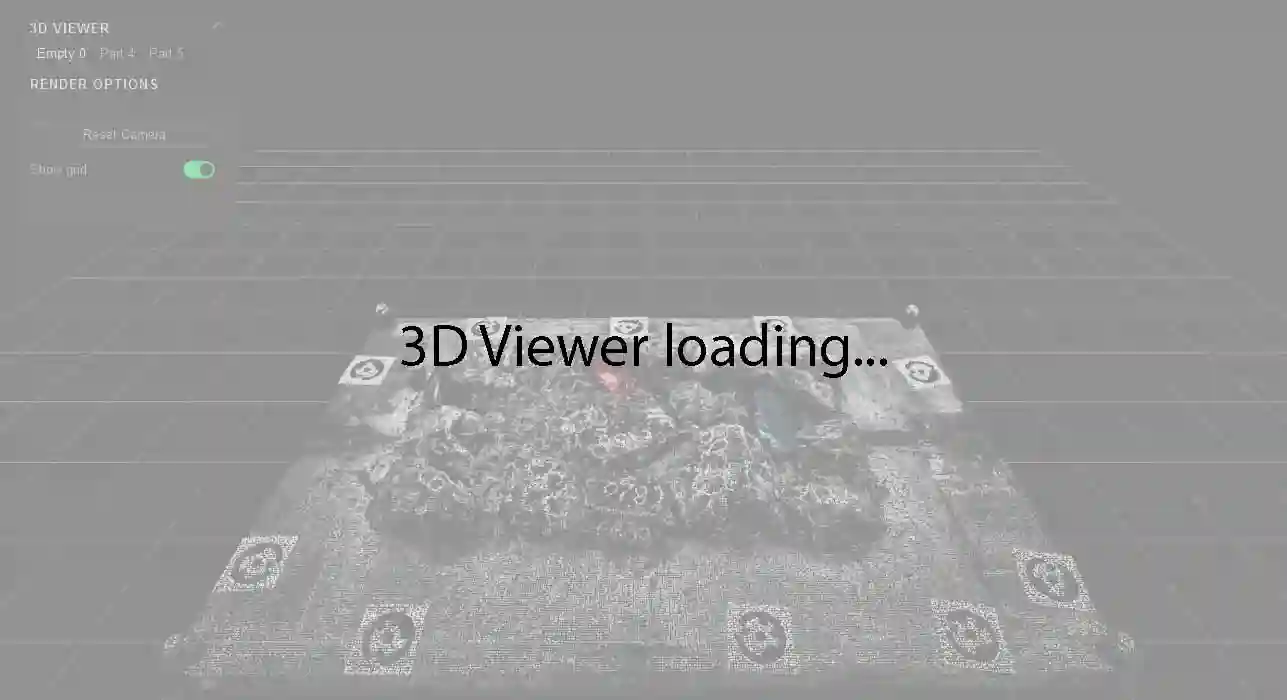
Stacking algorithm: Towards robotic construction
Dry stone masonry complements and enhances the worldwide landscape, in the form of retaining walls, arch bridges, towers, and fortifications. We aim at developing a construction robot that is capable of building such structures. To this end, a stacking algorithm is proposed to place stones in sequence and form a dry-joint masonry wall, no matter whatever shape and size of the stones given.
The proposed algorithm is a combination of artificial intelligence and mason’s rules-of-thumb. We translate mason’s practices into a set of nonlinear equations, including maximising the geometric similarity of the stone shape and the base shape, minimising the potential energy of stones, and prioritising placement from boundaries. The best position and pose of a stone are found by solving an optimization problem formulated from the above equations. We aim to find the solution from all possibilities. The stone can be moved into the bounding volume of the target wall with any pose, as long as it does not violate stones that are already in place.
Such freedom leads to an enormous amount of possible combinations of position and pose. To efficiently find the solution, we use a heuristics optimization solver, which is used to generate 3D mortar-joint masonry geometric models . We also use spherical harmonics to simplify the stone mesh given, which allows fast evaluation of each stone and accelerates the optimization process. Moreover, we analyse the dynamics of stones using the discrete element modelling method, to guarantee the stability of placement under gravity.
We show here one example of a stacked wall. You can go through the construction process by sliding the bar on the bottom. The generated stone wall resembles traditional dry stone masonry in the sense that the facades and corners tilt towards the interior and that interlocking can be found in all directions.
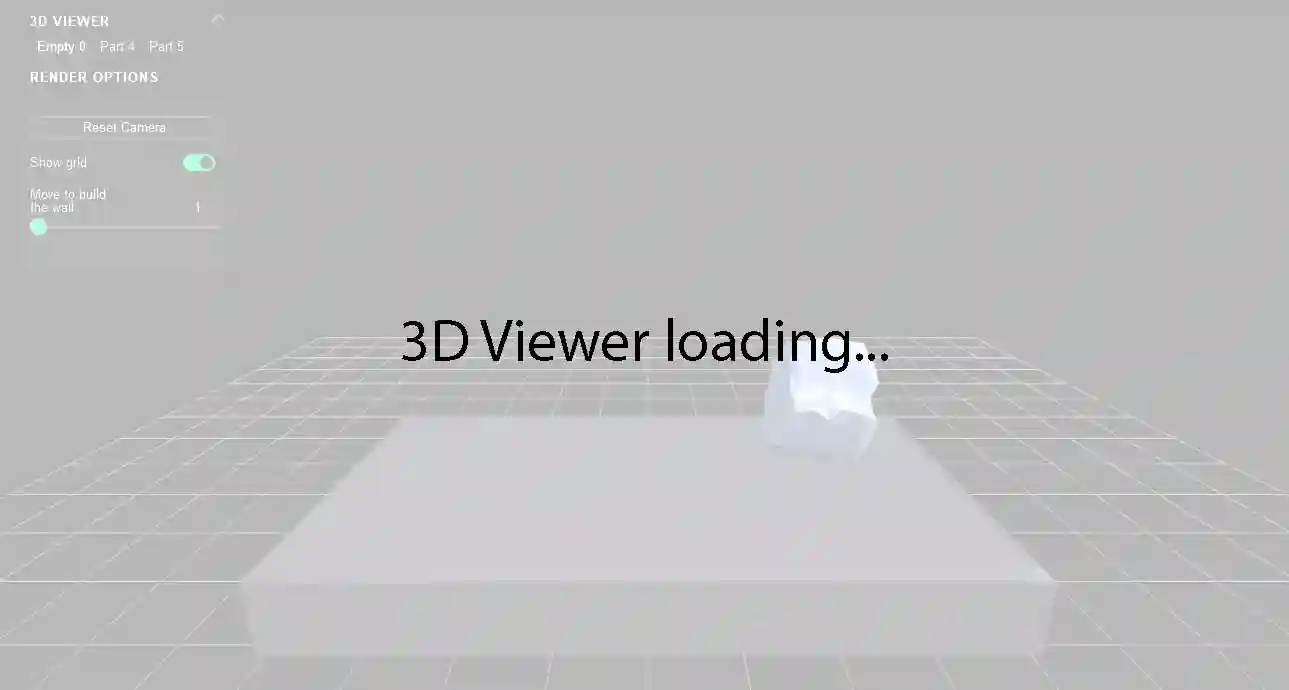
AR Assembly
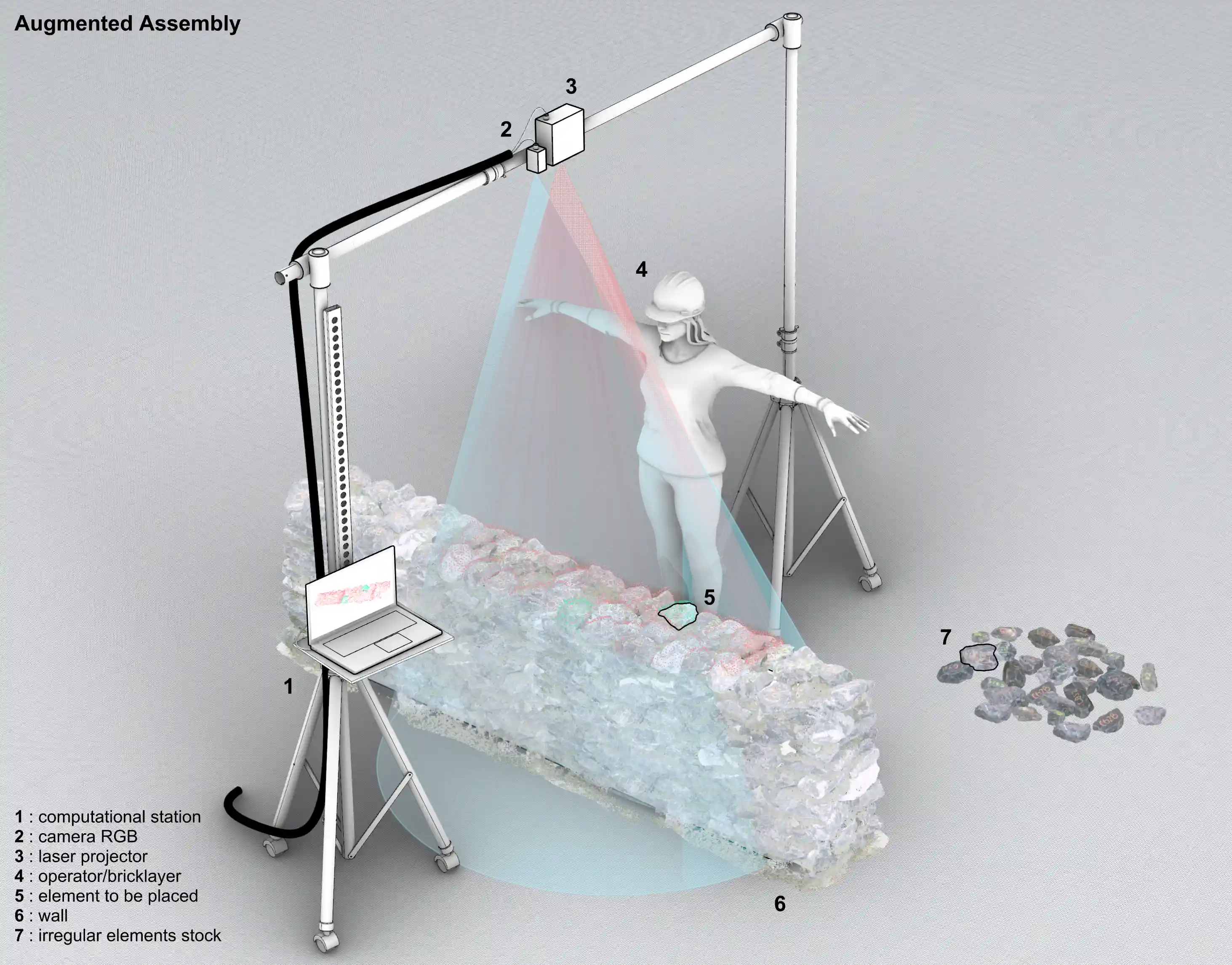
We explored a digital alternative to dry stone stacking where human operators are assisted to their stacking tasks by computed feedbacks able to guide the user for the correct placing of irregular stones without the need for trimming them before placement.
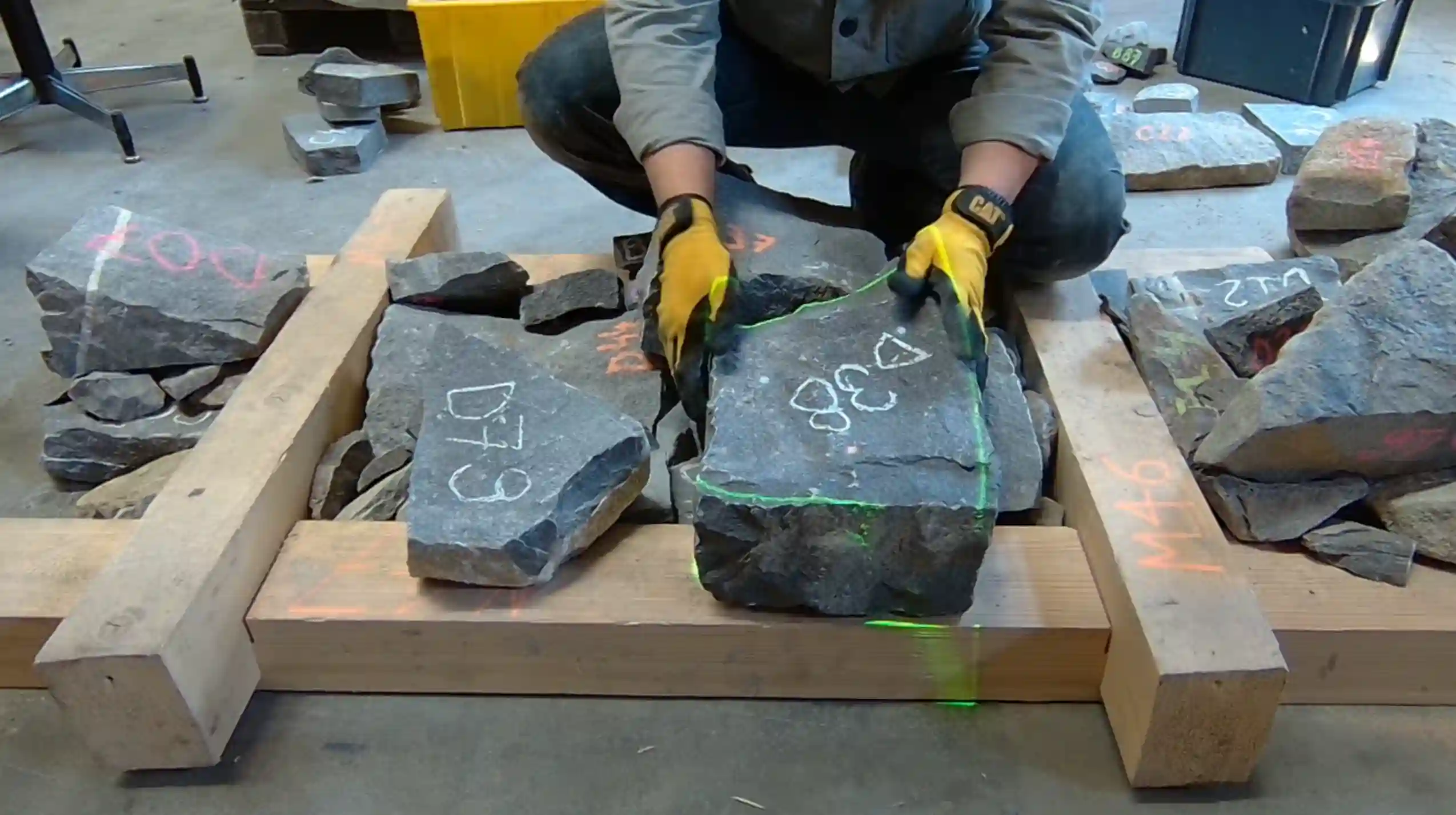
The feedback between the building area, the digital monitoring and vice versa is assured by a 3D camera and a projector. The user follows the visual hints in order to place the physical stone according to the 3D model computed on-the-fly. If the placement is successful, the user places the next stone. The pilot study for Augmented Stacking is currently under development and more information about it will be published soon.
Timber-lace dry stone construction is typically labor intensive and requires highly skilled builders. Besides the common heuristics of dry-stone masonry, masons need to carefully select their stones, trim them to the correct shape and finally adjust them to the wall configuration. To achieve a proper result in this phase, a consistent amount of time is necessary during the assembly.
The designed augmented system integrates in fact a stacking algorithm able to compute the pose of any given irregular shape and output its position in a given bounding box corresponding to the wall's boundaries. The stacking algorithm poses are converted to user interface projected to the working space.
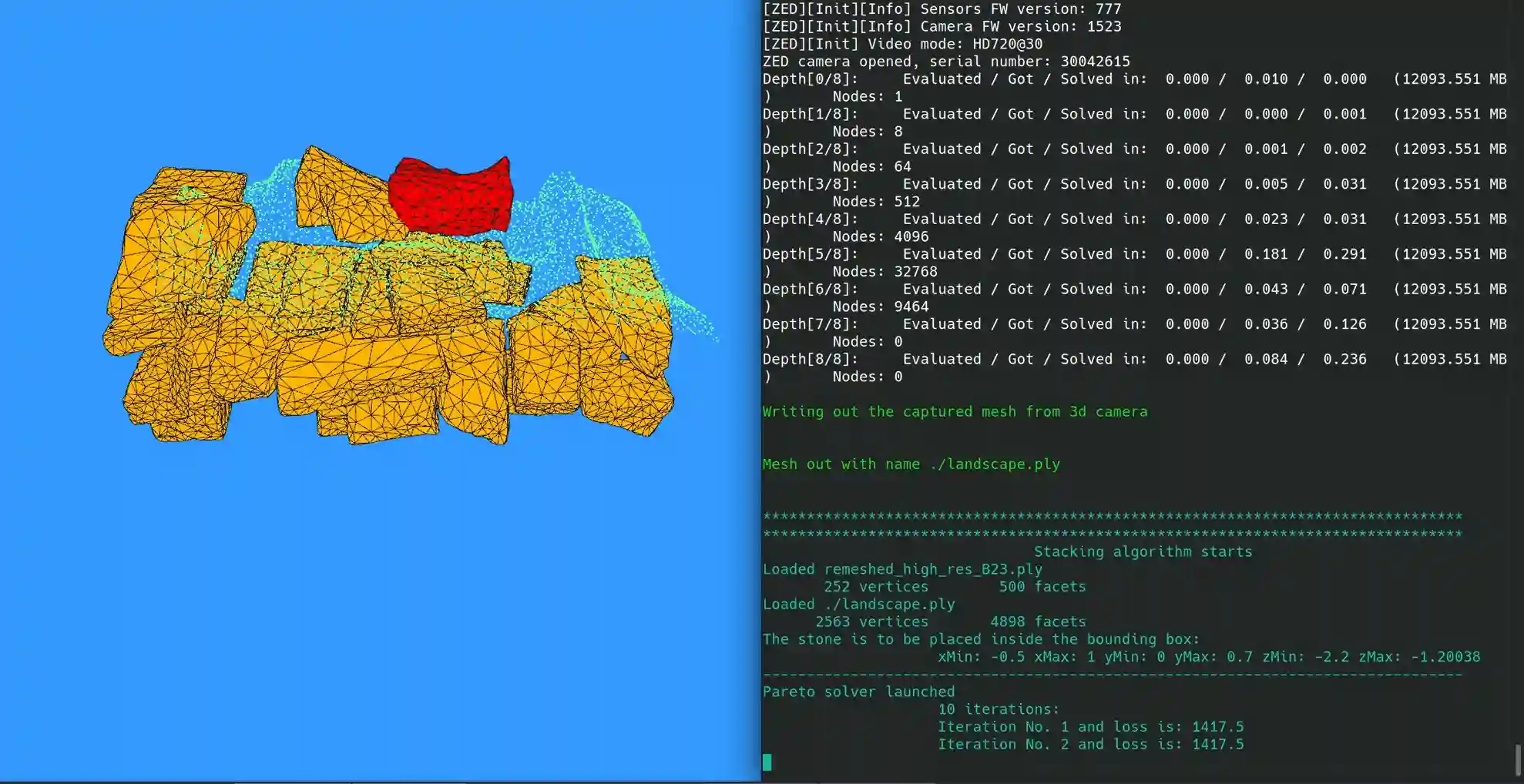
FURTHER INVESTIGATIONS
Now that we are able to digitize and replicate this type of construction technique, many explorations are still needed:
- How can we predict the structural capabilities thanks to digital models?
- Can structural capacities and other functions (waterproofing, insulation, etc.) be improved to meet the increasingly demanding requirements of modern buildings?
- What logistics can be implemented (prefabrication, transport, supply, quality, etc.) to make this technique more accessible and widespread?
All these questions will feed our future research, stay tuned!
Contributors
-
Main contributors:
IBOIS
,
EESD
,
MANSLAB
- Team: Julien Gamerro, Nicole Nay, Mahmoud Shaqfa, Andrea Settimi, Qianqing Wang, David Rebiffé, Basil Merz, Léo Benjamin
-
Assistance for image analysis:
Image Analysis Hub at EPFL Center for Imaging
- Team: Edward Andò
- Assistance for experimental facilities: The Structural Engineering Group (GIS) at EPFL
-
Website:
ENAC-IT4R
- Team: Charlotte Weil, Kirell Benzi Sylvain Tauxe, Pierre Guilbert